To ensure the quality of medical devices, the FDA (Food and Drug Administration) has laid down design control regulations for medical device manufacturers by incorporating them into the Quality System Regulation, 21 CFR Part 820. These design controls are established to maintain the required regulations and the quality aspects of medical devices, such as safety, performance, as well as product dependability related to software, hardware, services, or processed materials during the design and development phase. An effective implementation of these design controls lies in applying procedures and practices that comply with the regulations while meeting technical specifications of the product.
Application Procedures of Design Controls
Design controls can be used in any medical product development process. The application process of design controls is illustrated in the below figure.
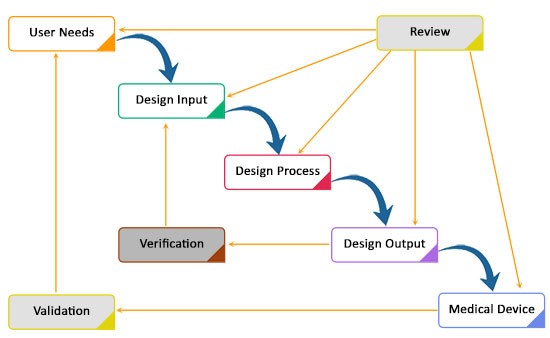
The development process shown in the above diagram is a traditional waterfall model. It is a basic logical sequencing of phases or stages of medical device design. The requirements are developed at the initial stage of the cycle and the device is designed to meet these requirements. Once the device is manufactured after the evaluation, feedbacks are collected between the next phase and previous phases, which represent an iterative nature of the development.
RELATED BLOG
The waterfall model is useful for the introduction of design controls, but the usefulness in practice is limited. Since this model follows a traditional or linear approach (starting from requirements and then moving to design implementation), it is difficult for device manufacturers to accommodate changes in design as per requirements. Also, the waterfall model may be applied to the development of simpler devices. For complex devices, a concurrent engineering model is more beneficial for the design processes in the industry since the concurrent process encourages simultaneous development and prompt changes, allowing for a more evolutionary approach to design.
Implementing Concurrent Approach in Design Control
Concurrent engineering assures that the device service and production personnel are involved throughout the process of development for the mutual optimization of the device and the related processes. The advantages of concurrent engineering are shorter development time, reduced production cost, and improved product quality.
Concurrent engineering includes a range of practices and techniques. The device development usually requires comprehensive reviews and approvals. Here are the processes of Design Controls applied in concurrent engineering.
Processes of Design Controls
Design and Development Planning
Design and development planning is the initial stage of the medical device development process and is used to ensure that the design is controlled appropriately and the quality objectives of the device are met. The plans must be consistent with the requirements of design control.
Planning also enables management to have more control over the design and development process by communicating policies, procedures, and goals more clearly to the members of the development team. It also provides a basis for measuring conformance to quality system objectives.
Design Input
The physical structure and the performance requirement form the basis of a device design and this process is called design input.
The starting point of a product design is Design Input. Developing requirements is the most important factor of design input, which forms the design tasks that are to be followed for the validation of the design. This is the reason why development of the requirements is the single most important design control activity followed by design input.
Design Output
The result of each design phase and the total design effort at the end of product development is called design output. The master record is formed on the basis of design output. The final design output consists of device, packaging, and labeling and the master record of the device.
Design output should be expressed in terms that allow satisfactory evaluation of conformance to design input requirements and should identify the characteristics of the design that are crucial to the safety and proper functioning of the device. This raises some fundamental issues for developers:
- What forms design output?
This issue is important because voluminous records are produced from a typical development project, some of which may not be categorized as design output and design output must be reasonably comprehensive to be effective.
- Are the form and content of the design output suitable?
An item may be considered as design output if it defines, describes, or elaborates an element of the design implementation. Examples include flowcharts, block diagrams, software code, and system or subsystem design specifications. The design output in one stage can sometimes be a part of the design input of subsequent stages.
DOWNLOAD WHITE PAPER: A Definitive Guide to Medical Device Design and Development Download Now
Design Review
Design review means a comprehensive, documented, and a systematic examination of the design. This will help in determining the adequacy of the design requirement and also in evaluating the capability of the design to meet these requirements and to identify problems.
Many types of reviews occur during the course of developing a product. Reviews may have both an internal and external focus. The internal focus is on the feasibility and produceability of the design with respect to support and manufacturing capabilities, whereas the external focus is whether the device design is viewed from the perspective of the user.
Design Verification & Validation
Validation is the process of making sure that user needs are met without any objective interference. The usual process to follow in order to validate a device could be inspections and analysis in some cases. However, the main goal of validation is to make sure that the device should provide the intended medical benefits in actual use condition. Validation is a cumulative effort to assure that the design will conform with user needs and intended use.
Design verification is a process of making sure that specific requirements are met during the product development. It also includes a detailed examination of design aspects at various stages in the development.
Design Changes
Design controls, if implemented properly can reduce product defects and increase end-user satisfaction. There are two principal elements involved in design changes:
- Document control: It is a process of tracking the status of documents and revision history one by one. The term “document” here includes all design documents, drawings, and other items of design input/output, which characterize some aspect of it.
- Change control: It is a process of tracking the corrective action arising from design review and verification prior to design transfer.
Design History File (Dhf)
Design history file (DHF) means a compilation of records which describes the design history of a finished device. Design control regulation mandates DHF, which illustrates the relationship between all the Design Controls. This is useful in tracing all changes throughout the product development process.
Conclusion
Design controls are a systematic way of controlling medical device design, which demonstrates the progress of product development efforts. Medical device product development must also follow a structured and methodical approach with traceability throughout the development process to ensure the device meets the required quality, safety, and performance standards.
eInfochips has extensive experience in developing FDA Class II and Class III devices for monitoring, wearable health, diagnostics & imaging, and telemedicine. We act as an innovation partner for many medical devices and pharmaceutical companies, including Fortune 500 firms to develop HIPAA compliant engineering solutions. Know more about medical devices engineering services.